The Power of a 5 axis CNC machine in Modern Machining
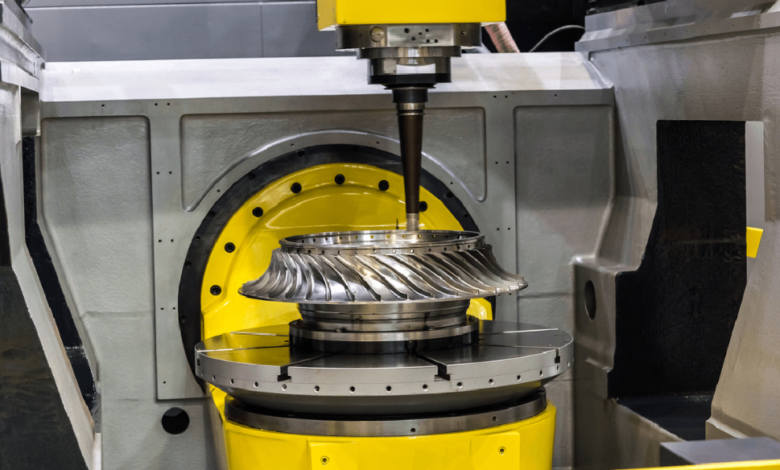
In today’s competitive manufacturing industry, precision, efficiency, and adaptability are the pillars of success. As design requirements grow more intricate and turnaround times shrink, traditional machining methods often struggle to meet expectations. That’s where the 5 axis CNC machine steps in, offering groundbreaking capabilities that reshape the production landscape.
This article explores the role of the 5 axis CNC machine, its inner workings, practical benefits, and why it has become the gold standard for high-precision, complex manufacturing.
What is a 5 axis CNC machine?
A 5 axis CNC machine is an advanced computer-controlled tool capable of moving a cutting instrument or the workpiece along five separate axes. These include the traditional three linear axes—X (left to right), Y (front to back), and Z (up and down)—along with two rotational axes, often labeled as A (rotation around the X-axis) and B (rotation around the Y-axis), or sometimes B and C.
This expanded motion capability allows the tool to approach the part from virtually any angle, making it ideal for creating complex geometries in a single setup.
How Does It Work?
At the core of every 5 axis CNC machine is a sophisticated control system that translates digital CAD/CAM designs into precise toolpaths. Once a design is finalized in computer-aided design (CAD) software, it’s processed in computer-aided manufacturing (CAM) software, which generates the instructions for machining.
These instructions, known as G-code, guide the tool as it simultaneously moves across five axes, adjusting its angle and depth to match the design. This process eliminates the need for manual repositioning, dramatically improving precision and efficiency.
Benefits of Using a 5 axis CNC machine
1. Machining in a Single Setup
Traditional 3-axis machines often require multiple setups to reach different sides of a workpiece. Each repositioning risks misalignment. A 5 axis CNC machine solves this by machining all surfaces in one operation, maintaining consistent orientation and improving accuracy.
2. Higher Precision for Complex Parts
From turbine blades to orthopedic implants, many components have curved surfaces or deep cavities. The 5-axis movement allows seamless cutting of these shapes with exceptional detail and consistency.
3. Time and Cost Efficiency
Fewer setups mean less downtime, reduced labor involvement, and faster part turnaround. This translates to lower operational costs and higher throughput in production environments.
4. Improved Surface Finish
Thanks to better tool orientation, the cutting edge maintains optimal contact with the surface, producing smoother finishes and reducing the need for post-machining polishing or grinding.
5. Extended Tool Life
Better cutting angles mean less strain on the tool. As a result, tools last longer, require less frequent replacement, and maintain their sharpness for more extended periods.
See also: How Low-Code Development Helps Reduce Technical Debt
Applications Across Industries
The versatility of a 5 axis CNC machine makes it a valuable asset across various sectors:
- Aerospace: Components like turbine blades, brackets, and housings demand precision and complex geometries, which are easily handled by 5-axis machines.
- Medical: Surgical tools and implants, especially those customized for patients, require high accuracy and detailed finishing.
- Automotive: Performance parts and intricate mold designs benefit from multi-angle machining capabilities.
- Energy Sector: The oil, gas, and renewable energy industries rely on custom parts with challenging dimensions and material properties.
- Prototyping and Research: Design engineers can quickly prototype and test new components with greater design freedom.
Types of 5 axis CNC Machines
Understanding the configurations available helps in selecting the right model:
• Head-Head Configuration
Both rotary axes are located in the machine head. This type allows for agile and dynamic movement, suitable for small, detailed workpieces.
• Table-Table Configuration
Rotary movement is built into the worktable. It provides stability and is preferred when machining larger or heavier parts.
• Table-Head Configuration
Combines one rotating axis in the head and one in the table, offering a balanced solution for flexibility and load-bearing.
Each type serves specific machining needs. The choice depends on the material, part complexity, and production volume.
How to Choose the Right 5 axis CNC machine
When considering a 5 axis CNC machine, assess the following factors:
• Size and Weight of Workpieces
Select a machine that accommodates your largest and heaviest parts comfortably without sacrificing movement freedom.
• Spindle Specifications
Different materials require different spindle speeds and torque. For example, aluminum may require high-speed spindles, while steel benefits from higher torque.
• Controller and Interface
User-friendly and reliable control systems like FANUC, Heidenhain, or Siemens improve productivity and operator ease.
• Software Compatibility
Ensure that your CAM software supports true 5-axis toolpaths and can simulate machining to prevent collisions or errors.
• Support and Maintenance
A reputable manufacturer or supplier should provide technical support, training, and replacement parts, helping you maintain uptime.
New or Used Machine?
✅ New Machine
- Equipped with cutting-edge features
- Comes with warranty and tech support
- Better suited for long-term production environments
✅ Used Machine
- Lower cost entry point
- Great for shops transitioning to multi-axis capabilities
- Needs careful inspection to ensure functionality
Regardless of the choice, a 5 axis CNC machine is a long-term investment with significant returns in efficiency and capability.
Challenges and Considerations
Although the 5 axis CNC machine is a powerful tool, it’s not without its challenges:
- Higher Initial Investment: The upfront cost is higher than conventional machines, though ROI is substantial over time.
- Complex Programming: Operators must understand multi-axis toolpaths, which require training.
- Maintenance Needs: With more moving parts, regular maintenance is essential to avoid downtime.
These are manageable concerns when supported by trained staff and reliable service providers.
Final Thoughts
The 5 axis CNC machine is more than just a technological upgrade—it’s a transformation in how we manufacture parts. With its ability to perform intricate tasks in a single setup, produce smoother finishes, and reduce lead times, it’s quickly becoming a necessity rather than a luxury.
As the demands of product innovation continue to grow, embracing advanced machining capabilities ensures you remain competitive in a high-precision market. Whether you’re producing aerospace components, custom medical devices, or automotive molds, a 5 axis CNC machine gives you the edge needed to lead in modern manufacturing.
Now is the time to take your shop to the next level—invest in precision, speed, and capability. Invest in a 5 axis CNC machine.